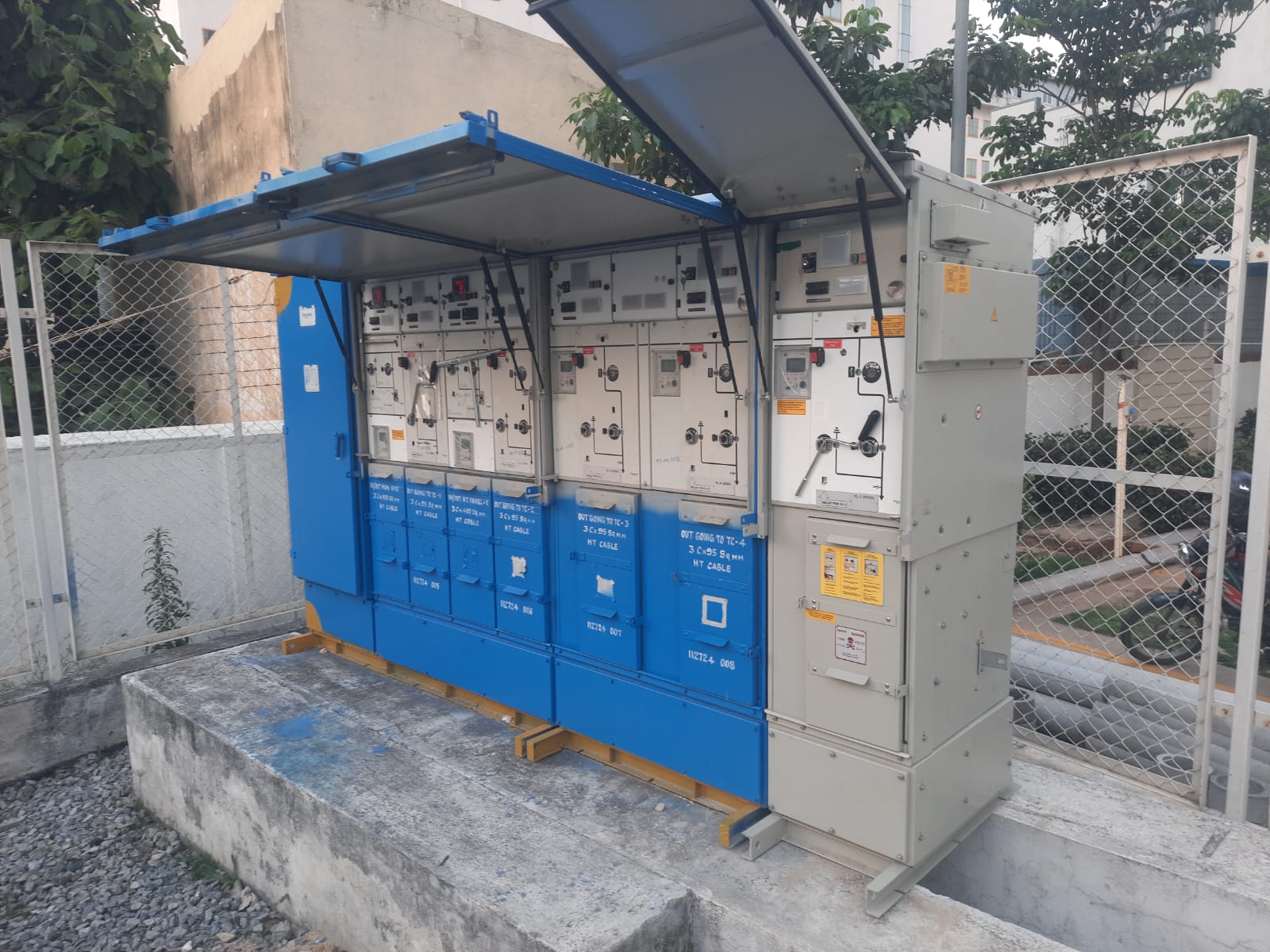
Maintaining a Ring Main Unit (RMU) is crucial for ensuring the reliability and efficiency of electrical distribution networks. This detailed guide covers the comprehensive steps and best practices for maintaining an RMU, ensuring its longevity and optimal performance.
1. Understanding Ring Main Units (RMUs)
Definition and Purpose
A Ring Main Unit (RMU) is a type of electrical switchgear used to manage the flow of electricity in a distribution network. It typically includes switches and circuit breakers that can control, isolate, and protect electrical circuits. RMUs are used in medium-voltage (MV) distribution networks to enhance reliability and provide operational flexibility.
Components of an RMU
- Circuit Breakers: These protect the electrical network from overloads and short circuits.
- Switches: Allow for the manual or automatic disconnection of circuits.
- Busbars: Conductive bars that distribute power to multiple circuits.
- Current Transformers (CTs): Measure the current and provide data for monitoring and protection.
- Voltage Transformers (VTs): Measure the voltage levels for monitoring and protection.
- Protection Relays: Devices that detect faults and initiate protective actions.
2. Importance of RMU Maintenance
Safety
Regular maintenance of RMUs ensures the safety of personnel and equipment. Properly maintained RMUs reduce the risk of electrical faults, which can cause fires, equipment damage, and injuries.
Reliability
A well-maintained RMU ensures a reliable power supply, minimizing downtime and service interruptions. This is especially important for critical infrastructure such as hospitals, data centers, and industrial facilities.
Efficiency
Maintaining RMUs improves the efficiency of the electrical distribution network. Proper maintenance helps in detecting and addressing issues before they escalate, leading to energy savings and reduced operational costs.
3. Maintenance Procedures for RMUs
Regular Inspections
- Visual Inspection: Conduct regular visual inspections to check for signs of wear and tear, corrosion, or physical damage to the RMU and its components.
- Thermal Imaging: Use thermal imaging cameras to detect hot spots that indicate potential problems such as loose connections or overloaded components.
- Cleaning: Keep the RMU and its surroundings clean to prevent dust and debris from interfering with the operation of components.
Electrical Testing
- Insulation Resistance Testing: Measure the insulation resistance of cables, busbars, and other components to ensure they are functioning correctly and not degrading.
- Dielectric Testing: Perform dielectric tests to verify the insulating properties of components and ensure they can handle the operating voltage.
- Contact Resistance Testing: Check the resistance of electrical contacts to ensure they are low and stable, indicating good connectivity.
Functional Testing
- Switch Operation: Test the operation of switches to ensure they can open and close correctly and smoothly.
- Circuit Breaker Testing: Test the tripping mechanism of circuit breakers to ensure they operate correctly under fault conditions.
- Protection Relay Testing: Test protection relays to verify their settings and functionality. This includes testing the trip settings and timing to ensure accurate fault detection and isolation.
4. Preventive Maintenance
Scheduled Maintenance
- Monthly Inspections: Conduct basic inspections every month to check for obvious signs of wear and tear or potential issues.
- Quarterly Maintenance: Perform more detailed inspections and tests quarterly, including cleaning, lubrication, and checking connections.
- Annual Maintenance: Conduct a comprehensive maintenance check annually. This should include all the tests and inspections mentioned above, as well as any manufacturer-recommended procedures.
Lubrication
- Switch Mechanisms: Lubricate the moving parts of switches to ensure smooth operation and prevent seizing.
- Circuit Breakers: Lubricate the moving parts of circuit breakers to ensure reliable operation and longevity.
Tightening Connections
- Busbars and Cables: Regularly check and tighten the connections of busbars and cables to prevent loose connections, which can cause overheating and faults.
- Terminals: Ensure all terminals are securely tightened to maintain good electrical connections.
5. Condition Monitoring
Online Monitoring Systems
- Real-Time Data: Implement online monitoring systems to collect real-time data on the performance of the RMU. This data can be used to detect anomalies and potential issues before they cause failures.
- Alarms and Notifications: Set up alarms and notifications to alert maintenance personnel of any abnormal conditions or faults detected by the monitoring system.
Offline Monitoring
- Periodic Testing: Conduct offline testing of components during scheduled maintenance to ensure they are functioning correctly.
- Data Analysis: Analyze the data collected from offline tests to identify trends and potential issues that need to be addressed.
6. Troubleshooting and Repairs
Fault Identification
- Visual and Thermal Inspections: Use visual and thermal inspections to identify obvious signs of faults such as burn marks, discoloration, or hot spots.
- Electrical Testing: Use electrical tests to pinpoint the location and cause of faults. This includes insulation resistance tests, contact resistance tests, and other diagnostic tests.
Component Replacement
- Switches and Circuit Breakers: Replace faulty switches and circuit breakers with new ones that meet the specifications of the RMU.
- Busbars and Cables: Replace damaged busbars and cables to ensure the integrity of the electrical connections.
- Protection Relays: Replace malfunctioning protection relays to ensure accurate fault detection and protection.
7. Documentation and Record Keeping
Maintenance Logs
- Inspection Records: Maintain detailed records of all inspections, including the date, findings, and actions taken.
- Test Results: Record the results of all electrical and functional tests, along with any corrective actions taken.
- Component Replacements: Keep a log of all components that have been replaced, including the date, reason for replacement, and details of the new components.
Maintenance Schedules
- Preventive Maintenance Schedule: Develop and maintain a preventive maintenance schedule that outlines the frequency and scope of all maintenance activities.
- Emergency Maintenance Procedures: Document procedures for emergency maintenance and repairs to ensure a quick and effective response to unexpected issues.
8. Training and Competency
Staff Training
- Technical Training: Provide technical training to maintenance personnel on the operation and maintenance of RMUs. This includes training on specific equipment and procedures.
- Safety Training: Ensure all personnel are trained in safety procedures and practices, including the use of personal protective equipment (PPE) and safe work practices.
Competency Assessments
- Periodic Assessments: Conduct periodic assessments of maintenance personnel to ensure they are competent and capable of performing their duties.
- Continuous Improvement: Provide opportunities for continuous improvement and professional development to keep personnel up-to-date with the latest technologies and best practices.
9. Safety Considerations
Personal Protective Equipment (PPE)
- Required PPE: Ensure all maintenance personnel wear the required PPE, including insulated gloves, safety glasses, and protective clothing.
- PPE Maintenance: Regularly inspect and maintain PPE to ensure it is in good condition and provides adequate protection.
Safe Work Practices
- Lockout/Tagout (LOTO): Implement and enforce LOTO procedures to ensure equipment is safely de-energized before maintenance work begins.
- Hazard Identification: Identify and mitigate hazards associated with RMU maintenance, such as electrical shock, arc flash, and falls.
10. Environmental Considerations
Environmental Protection
- Spill Prevention: Implement measures to prevent and contain spills of oil, coolant, or other hazardous materials used in RMUs.
- Waste Management: Properly manage and dispose of waste materials generated during maintenance activities, including used oil, filters, and damaged components.
Sustainable Practices
- Energy Efficiency: Implement practices to improve the energy efficiency of RMUs, such as using energy-efficient components and optimizing load management.
- Recycling: Promote the recycling of materials used in RMUs, including metals, plastics, and electrical components.
11. Manufacturer Guidelines
Adhering to Recommendations
- Manuals and Guidelines: Follow the manufacturer’s manuals and guidelines for the operation and maintenance of RMUs.
- Warranty Compliance: Ensure maintenance practices comply with warranty requirements to avoid voiding warranties on equipment and components.
12. Technological Advancements
Upgrading Equipment
- Modernization: Consider upgrading RMUs with modern components and technologies to enhance performance and reliability.
- Smart Technologies: Implement smart technologies such as remote monitoring, automation, and advanced protection systems to improve the efficiency and reliability of RMUs.
13. Common Challenges and Solutions
Addressing Challenges
- Aging Infrastructure: Develop a plan for managing and upgrading aging RMUs to ensure continued reliability.
- Environmental Conditions: Implement measures to protect RMUs from harsh environmental conditions such as extreme temperatures, humidity, and corrosive environments.
- Resource Constraints: Optimize maintenance resources by prioritizing critical tasks and using data-driven maintenance strategies.
14. Case Studies and Best Practices
Learning from Examples
- Successful Implementations: Study successful RMU maintenance programs in similar industries to identify best practices and lessons learned.
- Continuous Improvement: Continuously improve maintenance practices based on feedback, data analysis, and advancements in technology.
15. Conclusion
Maintaining a Ring Main Unit is a critical task that ensures the reliability, safety, and efficiency of electrical distribution networks. By following the comprehensive maintenance procedures outlined in this guide, organizations can enhance the performance and longevity of their RMUs. Regular inspections, preventive maintenance, condition monitoring, and adherence to safety and environmental considerations are key to successful RMU maintenance. Additionally, ongoing training and continuous improvement efforts will help maintenance personnel stay competent and up-to-date with the latest practices and technologies.