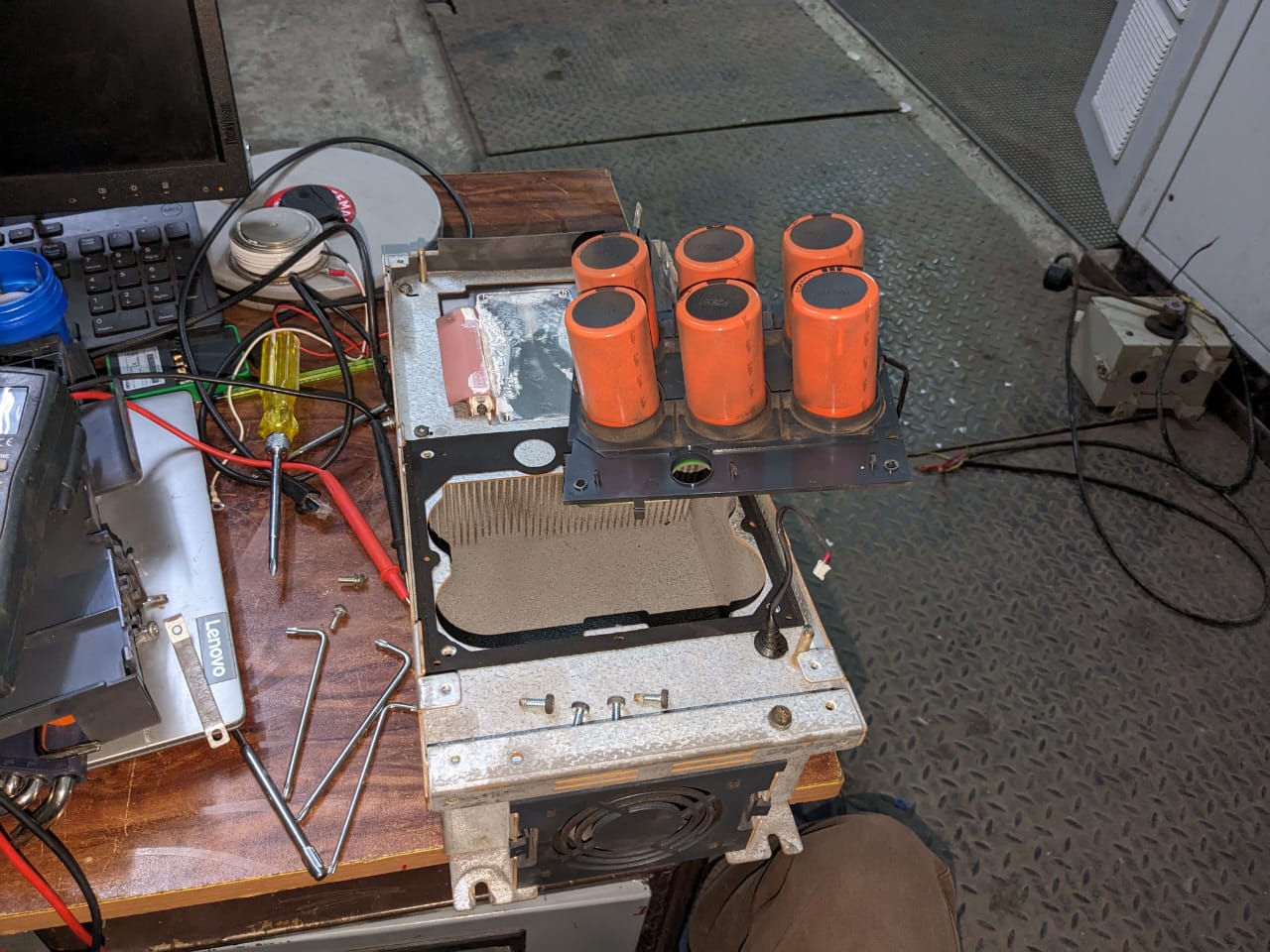
Welcome to our informative article on the most dangerous fault in Variable Frequency Drives (VFDs). VFDs are an integral part of many industrial applications, providing efficiency and cost savings. However, like any equipment, they are susceptible to faults that can pose risks to safety and production. In this section, we will discuss the most dangerous fault in a VFD and provide essential fixes to mitigate these risks.
Key Takeaways
- The most dangerous fault in a VFD can pose risks to safety and production.
- It is essential to identify the specific fault, understand the risks, and take preventive measures to avoid costly downtime and equipment damage.
- Regular maintenance and safe operating practices are crucial for maintaining optimal VFD performance and preventing faults.
- Ensuring safety for VFD operation is a shared responsibility among manufacturers, operators, and technicians.
Understanding Variable Frequency Drives (VFDs)
Variable Frequency Drives (VFDs) are a type of motor controller that allows the speed and torque of an electric motor to be adjusted as required. VFDs achieve this by adjusting the frequency and voltage of the power supplied to the motor.
VFDs consist of three primary components: a rectifier, a DC bus, and an inverter. The rectifier converts AC power into DC power, which is stored in the DC bus. The inverter then converts the DC power back into AC power by determining the correct frequency and voltage required to meet the motor’s needs.
VFDs are commonly used in industrial settings where precise control of motor speed and torque is important. They are used in a wide range of applications, such as conveyor systems, pumps, fans, and mixers, among others.
By using VFDs, companies can achieve greater energy efficiency and reduce operating costs. This is because VFDs allow motors to operate at their optimal speed, rather than running continuously at full speed, which can result in energy waste and unnecessary wear and tear on the motor.
Identifying the Most Dangerous Fault in a VFD
One of the most critical aspects of VFD maintenance is identifying and addressing the most dangerous fault, which poses significant risks to both personnel and equipment. Here, we will discuss the specifics of this fault and how to identify it promptly, reducing the likelihood of production downtime and extensive repairs.
The dangerous fault in a VFD pertains to the DC link circuit, where an open connection can trigger a high-voltage fault, putting equipment and personnel in danger. The fault can be identified through a series of symptoms, including erratic motor behavior, tripping of the inverter, or alarms indicating DC bus or overvoltage issues. Consulting a professional technician is highly recommended, as they can use diagnostic tools and techniques to accurately identify and address the fault.
It is crucial to address the dangerous fault promptly. Failure to do so can result in severe consequences, including equipment damage, production downtime, and employee injuries. Addressing the fault as soon as it is detected can also prevent it from worsening, potentially reducing the extent of repairs required down the line.
Key Risks Associated with the Most Dangerous Fault in a VFD
Ignoring the most dangerous fault in a VFD can lead to significant risks that can compromise safety, damage equipment, and cause production downtime. Let’s take a closer look at some of the key risks that can arise from this fault:
Risks | Description |
---|---|
Electrical hazards | When a VFD fails to regulate voltage, it can result in electrical arching, sparks, and short circuits that can lead to, serious injury or even death to personnel in proximity. |
Equipment damage | Faults can damage VFD components, such as diodes, capacitors, and transistors, leading to erosion, thermal fatigue, and degradation of the VFD capacitors. The system failure can escalate, leading to more extensive damage. |
Production downtime | A VFD failure can result in unplanned downtime, affecting production activities and leading to increased costs. |
By understanding these risks, we can make our VFD operation resilient to the potential negative impact that faults can have. In the next section, we will discuss the preventive measures that can be taken to mitigate the risks of the most dangerous fault in a VFD.
Preventive Measures to Mitigate the Risks
By taking preventive measures, we can mitigate the risks associated with the most dangerous fault in a VFD. Here are some essential steps and best practices to prevent or minimize the likelihood of this fault occurring:
Regular Maintenance
Regular maintenance is key, and it should include cleaning, inspection, and monitoring. It is recommended to follow the manufacturer’s guidelines and schedule maintenance activities regularly to detect any faults early.
Inspections
Regular inspections can reduce the risk of electrical hazards, equipment damage, and production downtime. It is crucial to inspect each component of the VFD, including the wiring, connections, cooling system, and control circuits.
Proper Installation Techniques
Proper installation techniques are vital to prevent the most dangerous fault in a VFD. It is essential to ensure the installation complies with the manufacturer’s recommendations and the National Electrical Code (NEC).
Note: Improper installation can lead to electrical hazards and damage to the equipment.
Training
Training is essential for safe and efficient VFD operation. It is recommended to provide training to staff and personnel who are responsible for the installation, operation, and maintenance of the VFD.
Safety Measures
Safety measures must be followed when operating a VFD to avoid potential hazards. These measures may include proper grounding, electrical protection, and personal protective equipment.
By following these preventive measures, we can mitigate the risks associated with the most dangerous fault in a VFD and ensure a safe and efficient operation.
Corrective Actions for the Most Dangerous Fault
Addressing the most dangerous fault in a VFD requires swift and effective corrective actions to ensure safety and prevent further damage. Here, we will provide a comprehensive guide outlining the necessary steps to take when this fault occurs:
Step 1: Identify the Fault
The first step in addressing the most dangerous fault in a VFD is to accurately identify the fault. Symptoms of this fault may include overvoltage, undervoltage, or excessive heat. A thorough inspection of the VFD is necessary to diagnose the issue.
Step 2: Initiate Safety Precautions
Prior to attempting any repairs, it is crucial to put appropriate safety measures in place. Ensure the VFD is completely isolated from power sources and electrical hazards are identified and mitigated. Use appropriate personal protective equipment (PPE) such as insulated gloves before handling any electrical components.
Step 3: Troubleshoot the Fault
Once the safety measures are in place, troubleshoot the issue by checking the power supply, wiring, and control board. To do this effectively, refer to the VFD manufacturer’s guidelines. Verify that all connections are secure, and no wires are damaged.
Step 4: Implement Repairs
After identifying the fault, following all safety precautions, and troubleshooting the issue, it’s time to implement necessary repairs. Depending on the nature and severity of the fault, repairs may include replacing damaged components, reconfiguring settings, or even replacing the entire VFD. Any repairs should be done following the manufacturer’s guidelines, and testing of the VFD should be done before putting it back in service.
Proper implementation of these corrective actions can help mitigate the risks associated with the most dangerous fault in a VFD, providing a safe and efficient operation.
Importance of Regular Maintenance for VFDs
Regular maintenance is crucial for the safe and efficient operation of Variable Frequency Drives (VFDs). By implementing a comprehensive maintenance program that includes routine inspections, cleaning, and monitoring, we can prevent the most dangerous fault in a VFD and ensure its optimal performance.
Regular inspections can help identify potential issues before they become major problems. During inspections, we should examine the equipment and check for any signs of wear and tear, loose connections, or abnormal sounds or vibrations. Regular cleaning can also help prevent issues by removing dirt, dust, and other contaminants that can build up and impair the equipment’s function.
Other essential maintenance tasks include checking the VFD’s firmware and updating it as necessary, monitoring the temperature, and ensuring that the VFD is properly grounded. We should also be sure to follow the manufacturer’s guidelines for recommended maintenance intervals and procedures.
Proper maintenance not only helps prevent faults but also extends the lifespan of the equipment, reduces the risk of downtime, and minimizes repair costs. By prioritizing regular maintenance, we can ensure the safe and optimal performance of our VFDs and avoid potential hazards.
Best Practices for Safe VFD Operation
Our focus so far has been on identifying the most dangerous fault in VFDs and taking steps to prevent and mitigate their risks. However, ensuring the safe operation of VFDs requires more than just addressing this fault. Here are some best practices for safe VFD operation:
- Proper training: Anyone operating or working with VFDs should receive adequate training to understand how to operate them safely and correctly. This includes knowledge of potential hazards and how to prevent them.
- Follow manufacturer guidelines: Always follow the manufacturer’s instructions for proper installation, operation, maintenance, and repair of the VFD to ensure safe and optimal performance.
- Implement adequate safety measures: Provide adequate safety measures such as protective equipment, warning signs, and barriers to minimize risks for workers and equipment. Regular safety audits are crucial to identify and address any potential weaknesses in safety measures.
- Regular maintenance: As we emphasized in the previous section, regular maintenance is critical for ensuring safe VFD operation. Regular inspection, cleaning, and monitoring of VFDs can prevent potential hazards and prolong their lifespan.
- Stay up-to-date with current best practices: Stay informed about new best practices for safe VFD operation and update your procedures and practices accordingly.
By following these best practices, you can ensure the safety of your workers and equipment, avoid potential hazards and downtime, and promote optimal performance of your VFD system.
Conclusion
As we have discussed throughout this article, understanding the most dangerous fault in a VFD and taking the necessary preventive and corrective measures is essential for maintaining safety and optimal performance in industrial applications. By following the guidelines and best practices we have outlined, you can minimize the risks associated with this fault and ensure a smooth and efficient operation of your VFD system.
Remember, regular maintenance and proper training are critical to preventing the most dangerous fault and promoting safe VFD operation. Always follow manufacturer guidelines and implement adequate safety measures to ensure the longevity and optimal performance of your VFD system.
Thank you for reading through this informative article. We hope you have gained valuable insights into VFDs and the most dangerous fault to be aware of. If you have any questions or would like to learn more, please do not hesitate to reach out to our team of experts.
FAQ
What is the most dangerous fault in a VFD?
The most dangerous fault in a Variable Frequency Drive (VFD) is a short-circuit fault. This fault occurs when two or more phases of the VFD’s output terminals come into direct contact with each other or with ground, causing a high current flow. It poses significant risks to personnel, equipment, and the overall operation.
What are the key risks associated with the most dangerous fault in a VFD?
The key risks associated with this fault include potential electrical hazards, such as electric shock and fire, which can endanger personnel and damage equipment. Additionally, a short-circuit fault can lead to significant production downtime, resulting in financial losses and decreased efficiency.
How can I identify the most dangerous fault in a VFD?
The most common symptoms of a short-circuit fault in a VFD include tripped circuit breakers, abnormal noises, burning smells, and a sudden loss of control or power. Proper fault identification requires comprehensive troubleshooting, including visual inspections, measurements, and in-depth knowledge of VFD operation.
What are the preventive measures to mitigate the risks of the most dangerous fault?
To mitigate the risks associated with a short-circuit fault, it is crucial to implement preventive measures such as regular maintenance, inspections, and proper installation techniques. Routine inspections can identify potential faults or deteriorating components, while proper installation techniques minimize the chances of a short circuit occurring.
What are the corrective actions for the most dangerous fault in a VFD?
When a short-circuit fault occurs in a VFD, immediate corrective actions should be taken. These actions include isolating the faulted equipment, verifying the fault’s cause, repairing or replacing damaged components, and conducting thorough tests to ensure proper functionality before re-energizing the system.
Why is regular maintenance important for VFDs?
Regular maintenance is essential for VFDs because it helps identify and address potential faults, including the most dangerous fault, before they lead to extensive damage or unsafe conditions. Maintenance activities include cleaning, inspections, lubrication, and tests to ensure optimal performance and prolong the lifespan of the VFD system.
What are the best practices for safe VFD operation?
To ensure safe VFD operation, it is important to follow best practices such as proper training for personnel operating or working near VFDs. Adhering to manufacturer guidelines for installation, operation, and maintenance is crucial. Additionally, implementing adequate safety measures, including protective barriers and safety interlocks, enhances overall safety.
hi