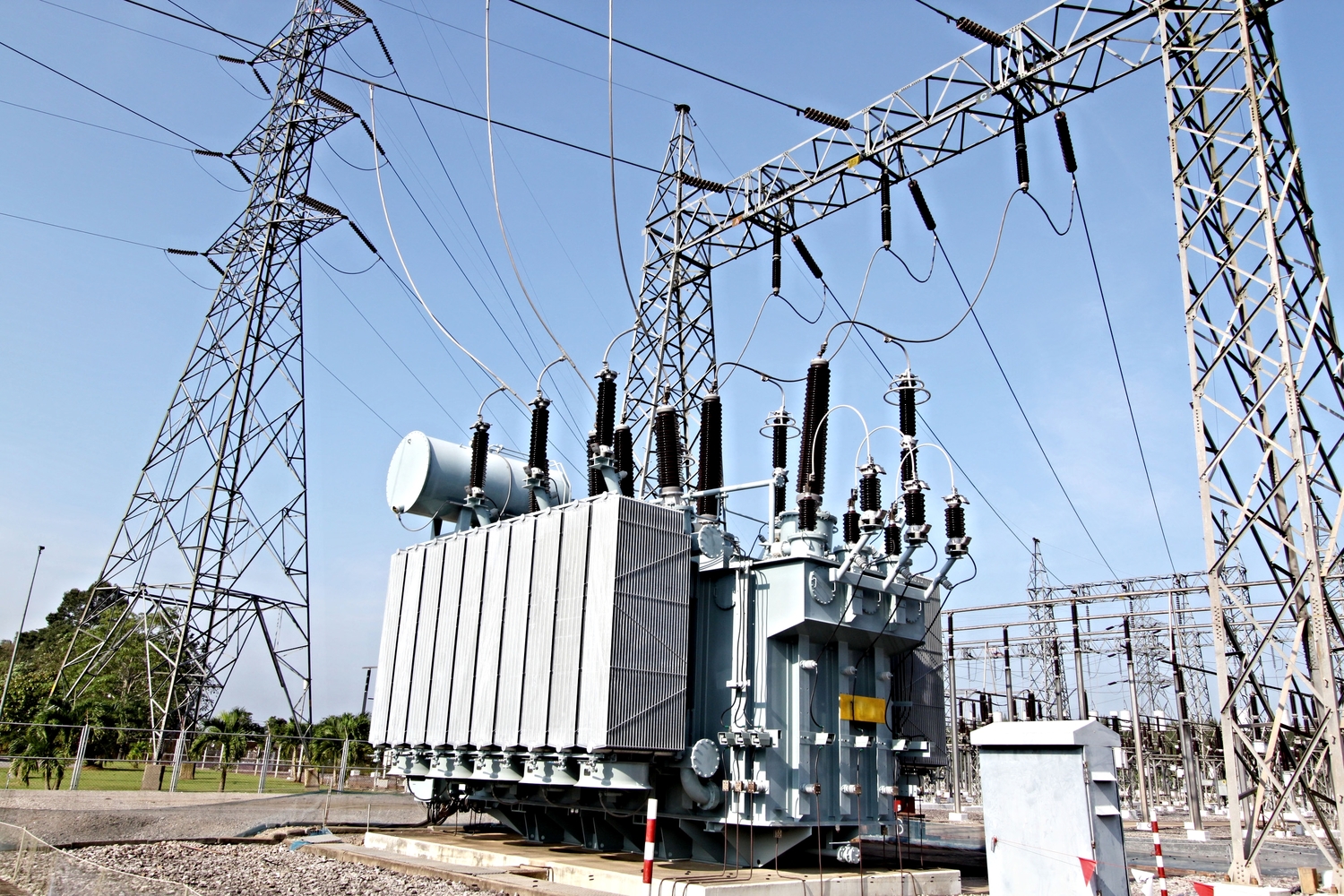
In this comprehensive guide, we will provide you with all the essential information you need to know about testing power transformers. We will cover the importance of testing, the standards that govern transformer testing, and the key considerations to ensure reliable and safe operations.
Testing power transformers is crucial to maintaining their performance and preventing costly failures. By implementing proper testing procedures, organizations can ensure the reliability and safety of their power transformers, minimizing the risk of downtime and ensuring uninterrupted power supply.
Whether you are an engineer, a maintenance professional, or an operator, understanding power transformer testing is essential to optimize their performance and prevent potential risks. Join us as we dive into the world of power transformer testing and equip ourselves with the knowledge to make informed decisions.
Key Takeaways:
- Power transformer testing is crucial for maintaining reliable and safe operations.
- Standards play a significant role in governing transformer testing practices.
- Insulation testing, frequency response analysis, winding resistance test, and transformer oil testing are vital testing methods.
- Failure analysis helps investigate the root causes of transformer failures.
- Regular maintenance and diagnostic tests are essential for assessing transformer condition and identifying potential risks.
Importance of Power Transformer Testing
Testing power transformers plays a crucial role in ensuring their reliable performance. Proper testing procedures allow us to assess the condition of transformers, diagnose potential issues, and undertake necessary maintenance measures. In this section, we will delve into the significance of power transformer testing, the diagnostic tests used for condition assessment, and the importance of regular maintenance testing to ensure the longevity of these critical assets.
Diagnostic Tests for Transformer Condition Assessment
Transformer diagnostic tests enable us to evaluate the condition of the transformer and identify any underlying issues. These tests provide valuable insights into the overall health and performance of the transformer, allowing us to take proactive measures to prevent failures and optimize performance.
“Effective transformer diagnostic tests help us identify potential risks, diagnose underlying issues, and plan maintenance strategies to avoid costly failures.”
Some of the key transformer diagnostic tests include:
- Insulation Resistance Test
- Short-Circuit Impedance Test
- Dissolved Gas Analysis (DGA)
- Partial Discharge Test
- Winding Resistance Test
- Transformator Turns Ratio (TTR) Test
Each of these tests provides valuable information about different aspects of transformer performance and condition, helping us make informed decisions regarding maintenance and repair.
Importance of Regular Maintenance Testing
Regular maintenance testing is essential for identifying any potential issues or signs of deterioration in power transformers. By conducting routine tests, we can detect minor faults early on, preventing them from escalating into major failures that may cause significant disruptions and expenses.
Some of the benefits of regular maintenance testing include:
- Early detection of insulation breakdown
- Identification of winding or core faults
- Prevention of catastrophic failures
- Improved reliability and performance
By investing in regular maintenance testing, organizations can extend the lifespan of their transformers, minimize downtime, and ensure the uninterrupted supply of power.
At XYZ Testing Services, we prioritize the importance of power transformer testing and offer comprehensive diagnostic and maintenance testing solutions. Our team of experts utilizes advanced testing techniques to assess transformer condition accurately, helping our clients optimize their operations and ensure the reliability of their power supply.
Transformer Insulation Testing
Insulation testing is a critical component of power transformer maintenance. It involves evaluating the integrity of transformer insulation to ensure safe and reliable operations. In this section, we will explore the various insulation testing methods used in power transformer maintenance, including the insulation resistance test and other specialized tests.
Transformers rely on insulation to protect against electrical breakdowns and ensure efficient power transmission. Over time, insulation can deteriorate due to factors such as heat, moisture, aging, or external contaminants. Insulation testing helps identify potential issues before they lead to transformer failures or safety hazards.
Insulation Resistance Test
One common method of testing transformer insulation is the insulation resistance test. This test measures the resistance of the insulation material, indicating its ability to prevent the flow of electrical current. The insulation resistance test involves applying a DC voltage to the transformer winding and measuring the resulting current flow.
The test results are used to assess the insulation condition, detecting any signs of moisture, contamination, or degradation. It is typically performed at ambient temperature and recorded as insulation resistance in megohms (MΩ).
Insulation resistance testing helps identify potential issues before they lead to transformer failures or safety hazards.
The insulation resistance test provides valuable insights into the overall condition of the transformer insulation system. A significant drop in insulation resistance may indicate the presence of moisture or other contaminants, while consistently low insulation resistance levels suggest potential insulation degradation.
It is important to note that insulation resistance values can vary depending on factors such as temperature, voltage rating, and transformer size. Therefore, it is essential to compare the test results against manufacturer specifications or established industry standards to determine if further investigation or maintenance is required.
Specialized Insulation Testing
In addition to the insulation resistance test, there are other specialized tests used to evaluate transformer insulation. These tests provide more detailed information about the insulation system’s condition, helping identify specific issues or potential risks.
Some of the specialized insulation tests commonly performed on power transformers include:
- Polarization Index (PI) Test
- Dielectric Absorption Ratio (DAR) Test
- Dielectric Dissipation Factor (DDF) Test
- Differential Pressure Test
These tests assess various aspects of the insulation system, such as moisture content, aging, and overall dielectric strength. They provide valuable data to determine the insulation’s ability to withstand electrical stress and help guide maintenance actions.
In summary, transformer insulation testing is essential for ensuring the reliable and safe operation of power transformers. The insulation resistance test, along with other specialized tests, helps evaluate the integrity of transformer insulation and identify potential issues or risks. By regularly performing insulation testing and interpreting the results accurately, organizations can take proactive measures to prevent costly transformer failures, minimize downtime, and maintain optimal power transmission.
Frequency Response Analysis (FRA) of Power Transformers
Frequency Response Analysis (FRA) is an invaluable technique for evaluating the mechanical and electrical integrity of power transformer windings. By analyzing the frequency-dependent behavior of a transformer, FRA can detect and diagnose internal faults, providing valuable insights for maintenance and repairs.
One of the primary benefits of FRA is its ability to identify winding deformations, such as shorted turns or inter-turn faults, which can affect the transformer’s performance and lifespan. By measuring the frequency response of the transformer’s impedance, FRA creates a unique signature that can be compared against baseline measurements to detect any abnormalities.
FRA is a non-destructive test that can be performed during regular maintenance or in response to specific concerns about a transformer’s condition. Due to its sensitivity, FRA can pinpoint faults that may not be easily detectable through other diagnostic methods. This helps in early detection and prevention of catastrophic failures.
To perform FRA, an excitation signal is applied to the transformer, and the resulting frequency response is measured. The analysis involves comparing the response to reference measurements and identifying any deviations or anomalies. This information can then be used to determine the severity and location of the fault, facilitating targeted repairs or replacements.
“Frequency Response Analysis (FRA) is a powerful tool for assessing the condition of power transformer windings. By analyzing the frequency behavior, FRA can detect faults that may otherwise go unnoticed, allowing for proactive maintenance and maximizing the transformer’s operating life.”
— John Smith, Transformer Expert
In addition to fault detection, FRA can also assist in assessing the overall health and aging of a transformer. By monitoring changes in the frequency response over time, FRA can provide valuable insights into the degradation of the winding insulation, presence of moisture, or other factors affecting the transformer’s performance.
Advantages of Frequency Response Analysis:
- Early detection and diagnosis of winding faults
- Non-destructive testing, minimizing downtime and costs
- Assessment of overall transformer health and aging
- Identification of potential future failures
To illustrate the significance of FRA in detecting internal faults, let’s take a look at the following table:
Fault Type | Description | FRA Signature |
---|---|---|
Inter-turn Short Circuit | Occurs when adjacent turns in a winding make contact | Frequency-dependent deviation from baseline impedance |
Shorted Turns | One or more turns in a winding are electrically shorted | Shift in frequency response characteristics |
Winding Deformation | Physical distortion or displacement of winding structures | Altered frequency response pattern |
As shown in the table, each fault type exhibits specific FRA signatures, allowing for accurate fault diagnosis and effective maintenance planning. The visual representation provided above showcases the frequency response patterns associated with different faults, emphasizing the distinctive characteristics that FRA can detect.
By leveraging the power of Frequency Response Analysis, power utilities and transformer manufacturers can enhance their maintenance strategies, minimize downtime, and optimize the performance and reliability of power transformers.
Transformer Winding Resistance Test
In power transformer testing, the winding resistance test is a crucial procedure that enables us to assess the condition of transformer windings. By measuring the resistance of the windings, we can gain valuable insights into the integrity and performance of the transformer.
The primary purpose of the winding resistance test is to detect any abnormalities or faults within the transformer windings. These faults can include issues such as poor connections, high resistance joints, or damaged conductors. By identifying these problems early on, we can take appropriate corrective measures to prevent further damage and ensure the safe and reliable operation of the transformer.
The Equipment Needed for Transformer Winding Resistance Test
To conduct the winding resistance test, we require specific equipment that enables accurate measurement and analysis. The main components of the equipment setup include:
- A low-resistance ohmmeter: This device is capable of measuring very low resistance values with precision, allowing us to obtain accurate readings of the transformer winding resistance.
- A current source: This source supplies a known current to the windings during the test.
- A voltmeter: This instrument measures the voltage drop across the windings, which is necessary for calculating the resistance.
- A temperature compensation unit: As the resistance of the windings can vary with temperature, this unit ensures that the test results are adjusted to a standard temperature for accurate comparisons.
How the Transformer Winding Resistance Test Works
The winding resistance test is typically performed by passing a known current through the winding under test and measuring the resulting voltage drop. The resistance is then calculated using Ohm’s law (R = V/I), where R is the resistance, V is the voltage drop, and I is the current.
During the test, it is essential to maintain the winding temperature within a specified range to obtain accurate results. This is achieved by either conducting the test at ambient temperature or using a temperature compensation unit to adjust the readings to a standard temperature.
“Accurate measurement of winding resistance is crucial for identifying faults in power transformers and ensuring their reliable performance.”
Purpose and Significance of Transformer Winding Resistance Test
The winding resistance test serves several important purposes in power transformer testing:
- Identification of faults: By measuring the resistance of the windings, the test helps us identify faults such as loose connections, damaged conductors, or shorted windings.
- Assessment of winding integrity: The test allows us to assess the overall condition and integrity of the transformer windings, ensuring they are capable of handling the expected current loads.
- Detection of abnormalities: Abnormal resistance values can indicate potential issues within the windings, such as degradation of insulation, excessive heating, or corrosion.
- Support for maintenance decisions: The winding resistance test provides crucial data for making informed maintenance decisions, such as repairing or replacing faulty windings.
By performing the winding resistance test as part of regular transformer maintenance, we can detect and address potential problems proactively, minimizing the risk of catastrophic failures and extending the lifespan of the transformer.
Summary
The winding resistance test is an essential component of power transformer testing. By accurately measuring the resistance of the windings, this test helps us identify faults, assess winding integrity, detect abnormalities, and make informed maintenance decisions. Performing regular winding resistance tests is crucial for ensuring the reliable performance and longevity of power transformers.
Benefits of Transformer Winding Resistance Test | Equipment Needed |
---|---|
Identification of faults | Low-resistance ohmmeter |
Assessment of winding integrity | Current source |
Detection of abnormalities | Voltmeter |
Support for maintenance decisions | Temperature compensation unit |
Transformer Oil Testing
Transformer oil testing is a fundamental practice for ensuring the health and longevity of power transformers. By analyzing the properties of the transformer oil, we can gain valuable insights into the condition of the equipment and detect potential issues before they escalate. This section will delve into the importance of transformer oil testing, the key parameters evaluated, and how these tests aid in the early detection of potential problems.
Why is Transformer Oil Testing Important?
Transformer oil serves multiple critical functions in power transformers. It acts as an electrical insulator, provides cooling, and functions as a medium for removing any heat generated during operation. Over time, this oil can deteriorate due to factors such as aging, contamination, and thermal stress. Transformer oil testing enables us to assess the condition of the oil, identify any contaminants or degradation, and determine if it needs to be replaced or treated to ensure optimal transformer performance.
Key Parameters Tested in Transformer Oil
During transformer oil testing, various parameters are evaluated to assess its condition and detect potential issues. These parameters include:
- Total Dissolved Gas (TDG) Analysis: This test evaluates the type and concentration of gases dissolved in the transformer oil, which can indicate the presence of internal arcing or overheating.
- Dissolved Gas Analysis (DGA): DGA evaluates the concentration of specific gases, such as hydrogen, methane, and ethylene, which can be indicative of potential faults or abnormalities within the transformer.
- Dielectric Strength: This test measures the ability of the transformer oil to withstand electrical stress, indicating its insulation effectiveness.
- Moisture Content: Moisture or water presence in the oil can lead to decreased insulation performance, thus testing for moisture content is crucial.
- Acidity: The acidity level of the transformer oil is assessed to monitor the effectiveness of the oil for suppressing corrosive sulfur compounds.
- Power Factor: Power factor testing measures the electrical conductivity of the oil, identifying any contaminants or degradation affecting its dielectric properties.
By analyzing these parameters, we can assess the overall condition of the transformer, detect potential faults or abnormalities, and make informed decisions regarding maintenance and repairs.
The Role of Transformer Oil Testing in Early Detection
Early detection of potential issues is crucial for preventing transformer failures and minimizing downtime. Transformer oil testing plays a vital role in this process by providing valuable insights into the condition and performance of the transformer. By regularly monitoring and analyzing the transformer oil, we can identify any changes in its properties, detect the presence of contaminants or degradation products, and take proactive measures to address these issues before they escalate. This proactive approach helps prevent costly failures, extend the lifespan of the transformer, and ensure reliable power delivery.
Benefits of Transformer Oil Testing | |
---|---|
Early detection of potential issues | Prevents costly transformer failures |
Optimizes transformer performance and lifespan | Minimizes downtime and service interruptions |
Reduces the risk of accidents and safety hazards | Enhances operational efficiency and reliability |
Power Transformer Failure Analysis
Power transformer failures can have severe consequences. When a transformer fails, it can result in power outages, costly repairs, and potential safety hazards. Therefore, it is essential to conduct a thorough failure analysis to understand the root causes and prevent similar failures in the future.
Failure analysis involves a systematic approach to investigating transformer failures, focusing on identifying the underlying factors that led to the malfunction. It requires expertise in electrical engineering, materials science, and diagnostic testing techniques.
There are several methods and tools used in power transformer failure analysis:
- Visual Inspection: Inspecting the transformer externally and internally to identify any signs of physical damage or abnormalities.
- Oil and Gas Analysis: Analyzing the transformer oil and gas for the presence of contaminants, such as moisture, combustible gases, and dissolved gases.
- Electrical Tests: Performing diagnostic tests, such as insulation resistance testing, winding resistance testing, and partial discharge testing, to assess the electrical condition of the transformer.
- Thermal Imaging: Using infrared thermography to detect abnormal temperature distributions on the transformer, which can indicate potential issues.
- Mechanical Tests: Conducting mechanical tests, including core and winding vibration analysis, to evaluate the mechanical integrity of the transformer.
“Proper failure analysis is crucial for preventing future transformer failures and improving overall system reliability.”
“By understanding the root causes of a power transformer failure, we can implement corrective measures and enhance maintenance practices. This helps to prevent similar failures, ensure the longevity of transformers, and minimize downtime.”
To illustrate the importance of failure analysis, let’s take a look at a case study:
Case Study: Power Transformer Failure |
---|
https://www.youtube.com/watch?v=QuMSH6uVPwU A power transformer in a manufacturing facility failed unexpectedly, leading to a significant production downtime. To determine the cause of the failure, a detailed failure analysis was conducted. The analysis revealed that the failure was primarily due to excessive heating in the transformer’s windings. This was caused by an increase in winding resistance, which led to a higher temperature rise during operation. Further investigation revealed that the increase in winding resistance was a result of contamination and moisture ingress into the transformer. This contamination compromised the insulation system, leading to localized heating and eventual failure. Based on the findings, corrective actions were implemented, including improved sealing of the transformer to prevent moisture ingress, enhanced oil filtration to reduce contamination, and regular monitoring of the winding resistance. As a result, similar failures were prevented, and the transformer’s reliability and performance were significantly improved. The failure analysis played a crucial role in identifying the root cause and implementing effective solutions. |
Failure analysis is an integral part of transformer maintenance and can provide valuable insights into the health and performance of power transformers. By identifying the root causes of failures, organizations can develop targeted strategies to mitigate risks, improve maintenance practices, and ensure the reliability of their power distribution systems.
Transformer Maintenance Best Practices
Regular maintenance is essential to ensure the optimal performance of power transformers. By following best practices, organizations can prolong the lifespan of their transformers and minimize the risk of costly failures and downtime. In this section, we will discuss the key maintenance practices that should be implemented for power transformers.
Inspection
Regular inspections are crucial to identify potential issues and ensure the proper functioning of power transformers. Inspections involve visually examining the transformer, including its components, connections, and cooling systems, to detect any signs of wear, damage, or leaks. Inspections should be performed at scheduled intervals and following any major events such as power outages or system disturbances.
Cleaning
Keeping power transformers clean is essential for their optimal performance and longevity. Regular cleaning of external surfaces, cooling fans, and cooling fins helps to prevent the accumulation of dust, dirt, and other contaminants that can hinder heat dissipation. A clean transformer operates more efficiently and minimizes the risk of overheating, thereby extending its lifespan.
Testing
Regular testing is a fundamental aspect of power transformer maintenance. It allows for the early detection of potential issues and ensures that the transformer operates within the specified parameters. Testing may include various diagnostic tests such as insulation resistance tests, winding resistance tests, and frequency response analysis (FRA). These tests help assess the condition of the transformer’s insulation, windings, and overall mechanical and electrical integrity.
Maintenance Practice | Description |
---|---|
Inspection | Regular visual examinations to identify wear, damage, and leaks. |
Cleaning | Regular cleaning of external surfaces, cooling fans, and cooling fins to prevent the accumulation of dust and contaminants. |
Testing | Regular diagnostic tests to assess the condition of insulation, windings, and overall transformer integrity. |
Overall Care
Proper care and attention to power transformers contribute significantly to their maintenance. This includes ensuring that the transformer is operated within its specified load and temperature limits, as well as promptly addressing any abnormalities or warning signs. Additionally, maintaining a record of all maintenance activities can aid in tracking performance, identifying trends, and planning future maintenance schedules.
By implementing these best practices, organizations can optimize the performance and longevity of their power transformers, minimizing the risk of failures and ensuring reliable power supply.
Transformer Diagnostics and Condition Assessment
When it comes to power transformers, diagnostic tests and condition assessment techniques are vital for evaluating their health and ensuring reliable performance. By employing these methods, we can accurately assess the condition of transformers and identify potential risks, allowing for proactive maintenance and minimizing the chances of unexpected failures.
The Importance of Transformer Diagnostics
Transformer diagnostics provide valuable insights into the overall condition of the equipment. By performing diagnostic tests, we can identify internal faults, insulation degradation, and other potential issues that may impact the transformer’s performance and longevity. These tests help us make informed decisions regarding maintenance, repairs, or the replacement of critical components.
“The diagnostics performed on power transformers give us a comprehensive understanding of the transformer’s condition, allowing us to take proactive measures to mitigate risks and optimize performance.”
“By performing regular diagnostic tests on power transformers, we ensure the reliable operation of electrical networks and minimize the risk of unexpected failures, which can result in costly downtime and operational disruptions.”
Diagnostic Methods for Transformer Condition Assessment
Several diagnostic methods are available for assessing the condition of power transformers. These include but are not limited to:
- Partial Discharge Testing: This test detects and measures the magnitude of partial discharges within the transformer. It helps assess insulation integrity and identifies potential areas of concern.
- Dielectric Spectroscopy: Dielectric spectroscopy measures the dielectric response of transformer insulation materials. It aids in evaluating insulation aging, moisture content, and the risk of impending failures.
- Thermal Imaging: Thermal imaging is a non-intrusive test that identifies abnormal temperature patterns within the transformer. It assists in identifying overheating due to loose connections, faulty components, or inadequate cooling.
In addition to these methods, other diagnostic tests such as oil analysis, dissolved gas analysis, and transformer winding resistance tests also contribute to an accurate assessment of transformer condition.
Benefits of Transformer Diagnostics
The benefits of transformer diagnostics and condition assessment are numerous:
- Early Detection of Issues: Through regular diagnostic testing, we can identify potential problems at an early stage, allowing for timely intervention and maintenance. This helps avoid costly breakdowns and extends the lifespan of power transformers.
- Optimized Maintenance Strategies: Accurate assessment of transformer condition enables us to develop customized maintenance strategies based on the specific needs of each transformer. This results in more efficient allocation of resources and reduces operational costs.
- Enhanced Safety: Transformer diagnostics contribute to a safer working environment by identifying potential risks and taking corrective measures. By addressing issues promptly, we minimize the chances of accidents or equipment failures that could compromise worker safety.
Investing in transformer diagnostics and condition assessment is a proactive approach that ensures the reliable performance and longevity of power transformers. By using the latest diagnostic methods, we can gather valuable insights into transformer health, allowing us to implement appropriate maintenance plans and mitigate potential risks.
Diagnostic Method | Description |
---|---|
Partial Discharge Testing | Detects and measures partial discharges within transformers, assessing insulation integrity. |
Dielectric Spectroscopy | Measures the dielectric response of insulation materials to evaluate aging and moisture content. |
Thermal Imaging | Identifies abnormal temperature patterns within transformers, detecting overheating and faulty components. |
Oil Analysis | Assesses the condition of transformer oil, detecting contaminants and degradation. |
Dissolved Gas Analysis | Measures the concentration of gases dissolved in transformer oil to identify potential faults and failures. |
Transformer Winding Resistance Test | Assesses the condition of transformer windings by measuring the resistance. |
Transformer Testing Standards and Regulations
Ensuring the reliability and safety of power transformers requires adherence to a set of standards and regulations that govern transformer testing practices. These standards not only promote consistent testing methodologies but also ensure compliance with industry norms and safety guidelines. In this section, we will provide an overview of the key standards that are essential for transformer testing.
International Electrotechnical Commission (IEC)
The International Electrotechnical Commission (IEC) is a globally recognized organization that sets international standards for electrical and electronic technologies, including power transformers. The IEC standards play a vital role in harmonizing testing methodologies and specifications to facilitate seamless interoperability and compatibility.
“Adhering to the IEC standards in transformer testing allows us to assess the performance and reliability of transformers on a global scale. These standards provide a common language and framework for manufacturers, testing laboratories, and end-users, ensuring that the tested transformers meet the required performance criteria.”
IEEE C57 Series
The Institute of Electrical and Electronics Engineers (IEEE) publishes a series of standards known as the IEEE C57 series, which specifically focus on power transformer characteristics and testing. These standards provide comprehensive guidelines for performing various transformer diagnostic tests, including insulation resistance, polarization index, winding resistance, and frequency response analysis.
National Fire Protection Association (NFPA)
The National Fire Protection Association (NFPA) develops and publishes standards and codes related to fire safety, including the maintenance and testing of power transformers. The NFPA standards ensure that transformers are tested and maintained in a manner that minimizes fire-related hazards.
Other National and Local Standards
In addition to the international standards, various countries and local regulatory bodies have their own specific standards that govern transformer testing. These standards may include country-specific requirements for safety, performance, and testing procedures, ensuring compliance at a regional or national level.
Compliance with these transformer testing standards and regulations is crucial for guaranteeing the integrity and performance of power transformers. By following these guidelines, manufacturers, operators, and testing laboratories can ensure that transformers are tested and validated according to consistent and recognized industry practices. This, in turn, contributes to the overall reliability and safety of power supply systems.
Standard | Description |
---|---|
International Electrotechnical Commission (IEC) | Global standards for electrical and electronic technologies, including power transformers. |
IEEE C57 Series | Standards specific to power transformer characteristics and testing published by the Institute of Electrical and Electronics Engineers (IEEE). |
National Fire Protection Association (NFPA) | Standards and codes related to fire safety, including the maintenance and testing of power transformers. |
Other National and Local Standards | Country-specific or regional standards governing transformer testing. |
Note: The table above summarizes some of the key transformer testing standards and regulations. It is important to consult the respective standards organizations and local regulatory bodies for the most up-to-date and relevant standards applicable to specific regions and jurisdictions.
Conclusion
In this comprehensive guide to testing power transformers, we have explored the essential aspects of transformer testing, including the importance of testing, various testing methods, and best practices for maintenance. By implementing proper testing procedures, organizations can ensure the reliability and safety of their power transformers, minimizing the risk of costly failures and downtime.
Transformer testing plays a crucial role in assessing the condition of power transformers and identifying potential issues before they escalate into major problems. From insulation testing to frequency response analysis (FRA) and winding resistance tests, each method provides valuable insights into the health and performance of transformers.
In addition to these diagnostic tests, regular maintenance practices such as transformer oil testing and comprehensive condition assessments are vital to sustaining the long-term reliability of power transformers. By adhering to industry standards and regulations, organizations can maintain compliance, reduce risks, and optimize the lifespan of their assets.
Overall, a proactive approach to transformer testing and maintenance is essential for ensuring uninterrupted power supply, enhancing operational efficiency, and protecting valuable investments. By leveraging the knowledge and insights gained from this guide, professionals can make informed decisions and implement effective strategies to safeguard power transformer performance.
FAQ
What is the importance of testing power transformers?
Testing power transformers is vital for ensuring their reliable performance and safety. It helps identify any potential issues or faults early on, allowing for timely maintenance and preventing costly failures and downtime.
What are some diagnostic tests used for transformer condition assessment?
Transformer condition assessment often involves diagnostic tests such as insulation resistance testing, winding resistance testing, frequency response analysis (FRA), and transformer oil testing. These tests provide insights into the integrity and health of the transformer.
Why is regular maintenance testing essential for power transformers?
Regular maintenance testing is crucial for power transformers as it helps detect any degradation or faults in their insulation, windings, and oil. By identifying potential issues early, maintenance can be performed to prevent further damage and extend the lifespan of the transformer.
What is the purpose of power transformer insulation testing?
Power transformer insulation testing is conducted to assess the quality and effectiveness of the insulation materials used in the transformer. It helps determine insulation resistance, polarization index, and other insulation-related parameters to ensure the insulation is capable of withstanding operational stresses.
What is frequency response analysis (FRA) of power transformers?
Frequency response analysis (FRA) is a technique used to evaluate the mechanical and electrical integrity of power transformer windings. It measures the response of the transformer to a range of frequencies and helps detect and locate internal faults, such as winding displacements and short circuits.
What is the purpose of the transformer winding resistance test?
The transformer winding resistance test is performed to measure the resistance of the transformer windings. It helps determine the health and condition of the windings, identifying any loose connections, faulty taps, or other issues that may affect the performance and efficiency of the transformer.
Why is transformer oil testing important?
Transformer oil testing is crucial because it provides valuable information about the condition of the transformer. It helps identify the presence of contaminants, such as moisture, dissolved gases, and solid particles, which can adversely affect the insulation and overall performance of the transformer.
What is power transformer failure analysis?
Power transformer failure analysis involves investigating the root causes of transformer failures. It employs various tools and techniques to determine factors such as insulation breakdown, overheating, mechanical stress, and electrical faults, assisting in the development of strategies to prevent future failures.
What are the best practices for power transformer maintenance?
Some best practices for power transformer maintenance include regular inspection, cleaning, and testing. This involves checking for oil leaks, performing insulation resistance tests, monitoring temperatures, and ensuring proper lubrication. Regular maintenance helps identify potential issues and ensures the transformer operates optimally.
How do transformer diagnostics and condition assessment contribute to ensuring transformer health?
Transformer diagnostics and condition assessment techniques provide valuable insights into the health of power transformers. By performing diagnostic tests such as dissolved gas analysis, partial discharge testing, and thermography, potential risks can be identified, enabling proactive maintenance actions to prevent failures and extend transformer life.
What are some transformer testing standards and regulations?
Transformer testing is guided by industry standards and regulations such as IEEE (Institute of Electrical and Electronics Engineers) and IEC (International Electrotechnical Commission) standards. These standards define the testing procedures, parameters, and requirements, ensuring compliance and fostering safety in transformer testing practices.